The horizontal directional drilling machine ( HDD machine) is a device that can lay pipes and cables underground without digging the ground. It is widely used in the laying construction of water supply, electricity, natural gas, gas, oil, and other pipelines. The directional boring machine is an integrated fully self-loading machine, which adopts a number of advanced control technologies such as a closed energy-saving circuit, electro-hydraulic proportional control, and load-sensitive control. YG also provides various types of drilling rigs such as water well drilling rigs, diamond core drilling rigs, and rotary drilling rigs for sale. Contact us to get a horizontal directional drilling machine price.
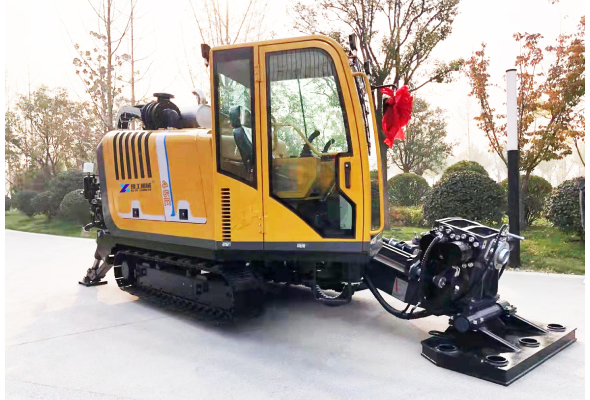
Hot Selling HDD Machine Parameters
Model | Weight | Engine power | Hole diameter | Construction distance | Machine size |
YG130 | 4750kg | 93KW | 750MM | 200M | 5465X1670X2040MM |
YG200 | 8200kg | 113KW | 900MM | 300M | 6750X2050X2400MM |
YG250 | 9000kg | 110KW | 1000MM | 300M | 6950X2160X2400MM |
YG320 | 10500KG | 154KW | 1100MM | 400M | 7300X2150X2250MM |
YG360 | 9500/10500KG | 153/154KW | 1200MM | 450M | 7300X2230X2310MM |
YG380 | 12800/14270KG | 179KW | 1300MM | 600M | 7300/8200X2250X2270MM |
YG420 | 13000KG | 179KW | 1350MM | 650M | 7300X2250X2270MM |
YG450B | 13500KG | 194KW | 1400MM | 700M | 7500X2250X2500MM |
YG450 | 14500KG | 194KW | 1500MM | 800M | 8450X2320X2650MM |
YG700L | 15000KG | 199KW | 1500MM | 900M | 9100X2280X2585MM |
YG900 | 15000KG | 239KW | 1500MM | 1000M | 10600X2260X2550MM |
YG900A | 21000KG | 264KW | 1500MM | 1000M | 10600X2260X2550MM |
YG12000T | 81TON | 2*565KW, 1*264KW | 2000MM | 3000M | 10600X2260X2550MM |
The above are the parameters of the hot selling HDD machine, please check. In addition, YG also provides water well drilling rigs, down-the-hole drilling rigs, Small DTH Hammer Drilling Rig, crawler drilling rigs, Mineral Exploration Drilling Rigs, and other drilling rigs. If you want to know more, please contact us.
HDD Machine Working Video
Horizontal Directional Drilling Machine Basic Structure
Whether it is a large or small horizontal directional drilling rig, the basic structure includes the main engine, drilling tools, steering system, mud system, and intelligent auxiliary system.
Host
The main engine directional drilling rig is the main body of the drilling operation through the equipment and the pulling back operation. The main engine is composed of the main engine of the drilling rig, the turntable, and other parts. The power system of the main engine is generally a diesel engine. As a power source, the diesel engine is one of the indicators to measure the construction capability of the drilling rig.
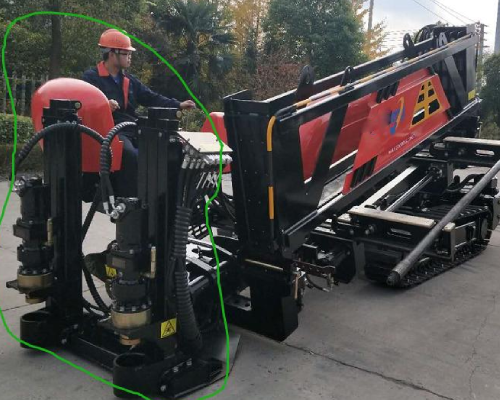
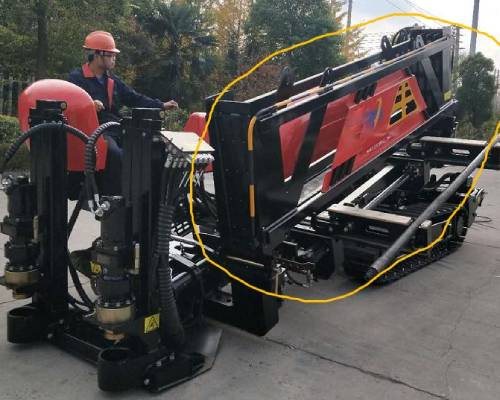
Drilling Tool
Drilling tools are various drilling tools used in the drilling and reaming of drilling rigs. These drilling tools generally include drill pipes, drill bits, reamers, cutting tools, etc. The drill pipe has the strength and flexibility of strands so as not to be twisted or broken during drilling. The drill bit is generally wedge-shaped. During the forward process, if the drill bit rotates continuously, the drilling trajectory is a straight line. There are many types of reamers, and different reamers can be selected according to different soil layers.
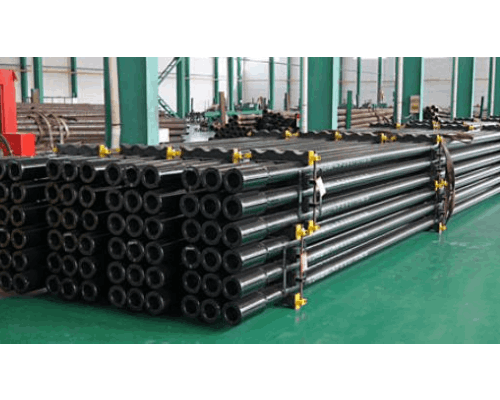
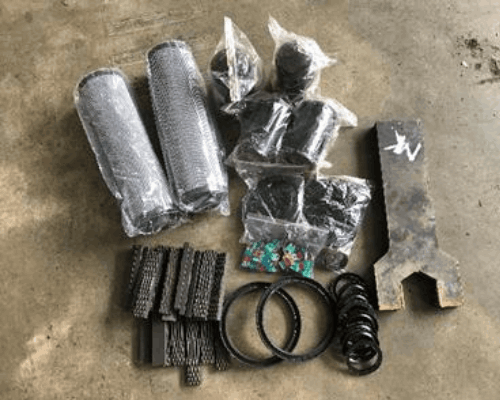
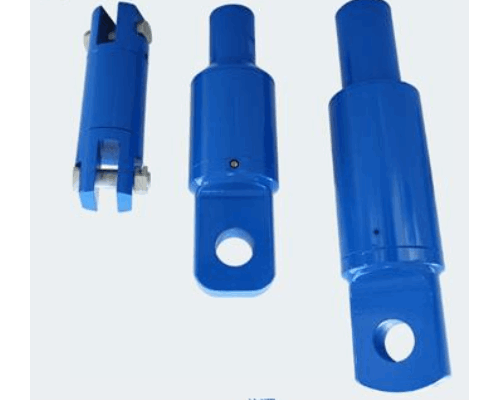
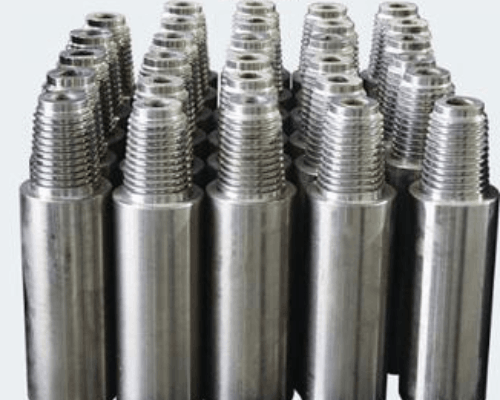
Guidance System
Guidance system plays an important role in the process of directional drilling, which includes wireless guidance systems and wired guidance systems. Wireless guidance systems are generally used during general drilling operations. When crossing rivers and lakes, because the ground is difficult to walk on or the drilling depth is too deep, the electromagnetic wave signal is difficult to accept, so a wired guidance system must be used.
Mud System
The mud system is an important piece of equipment to ensure the smooth progress of reaming and pipe pullback. In the process of drilling and reaming, the mud system can strengthen the soil layer and assist in drilling. The mud system consists of a mud mixing tank, a mud pump, and mud pipelines, which provide mud suitable for drilling conditions to the drilling rig system. Fully stir bentonite, water, and additives in the mud tank, pressurize the mud pump, spray out the drill pipe from the nozzle of the drilling tool, wash the atlas, and take away the cuttings, which plays the role of auxiliary drilling.
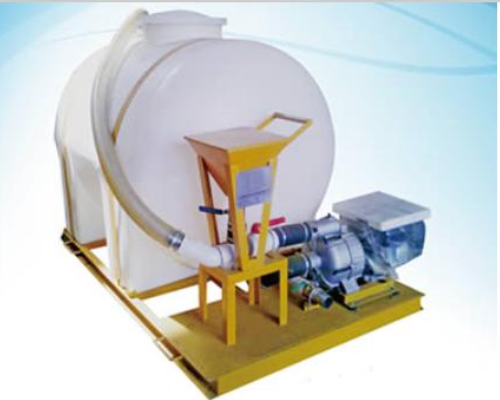
Intelligent Assistance System
The intelligent auxiliary system of horizontal directional drilling plays an important role in setting various parameters such as drilling depth, inlet and outlet positions, and pipe bending radius. These parameters can be adjusted according to the actual situation in the actual project.
Horizontal Directional Boring Machine Types
According to the diameter and length capacity of the laid pipeline, there are two types of horizontal directional drilling: small and large. Small horizontal directional drilling vise, power head double buoyancy technology, and high and low-speed push-pull rotation system can improve the adaptability of the drill pipe to working conditions and improve the construction efficiency of the drilling rig. Large-scale horizontal directional drilling adopts digital instrumentation, dual power system, and electronic sensing technology, which is convenient, safe, and fast for construction and operation.
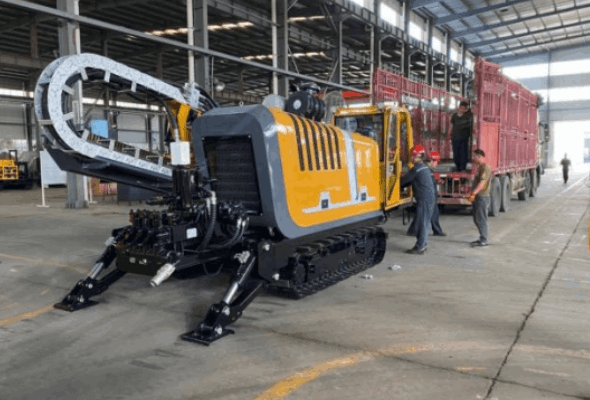
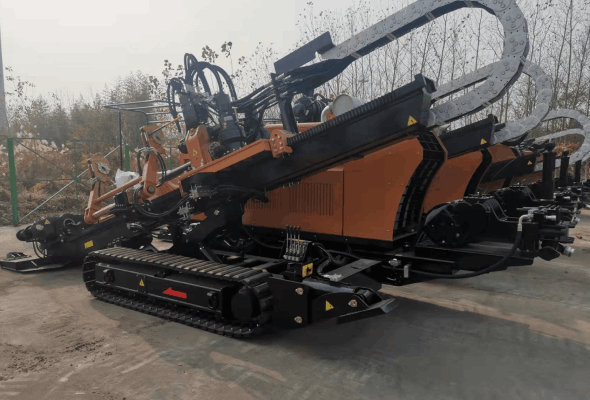
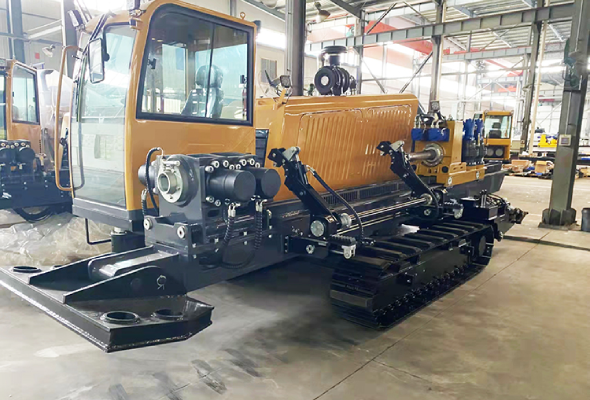
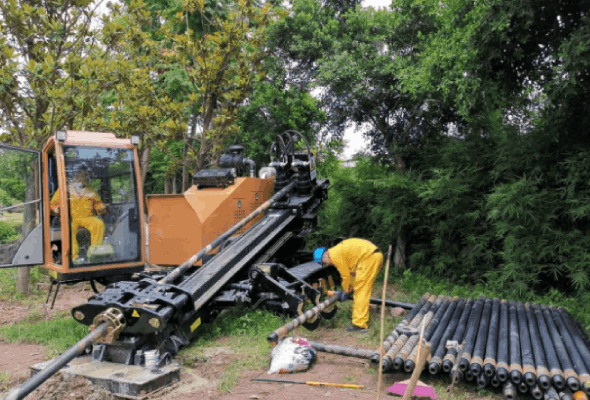
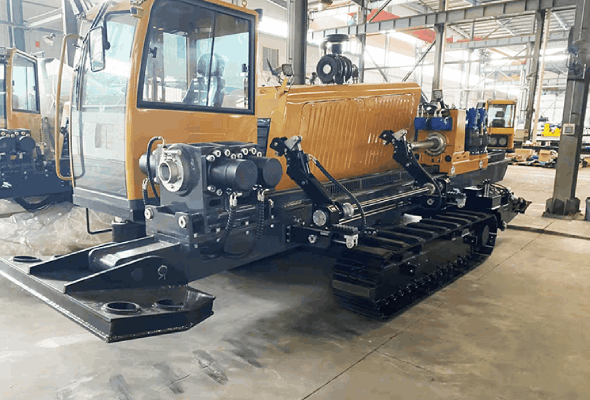
How Does the Horizontal Directional Drilling Machine Work?
The laying of pipelines using horizontal directional drilling mainly goes through three stages: drilling pilot holes, pre-expanding, and pulling back the pipeline.
Drill Pilot Hole
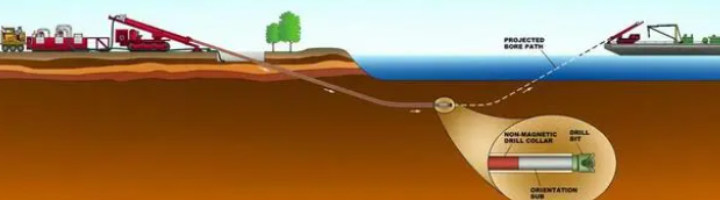
Position the drill pilot hole according to the pre-designed curve. Under the thrust of the drilling rig, the drill bit is driven to rotate and cut the stratum continuously. The drill is equipped with a positioning system. As a result, signals can be transmitted to engineers in real-time during the drilling process. Engineers can precisely control the precise coordinates of the drill pipe. If it is found that there is a deviation in the position of the drill pipe, it can be corrected in time so that the pilot hole always advances in the specified direction.
Pre-expansion
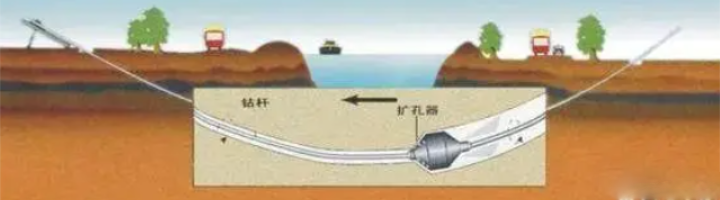
The second step is to pre-expand the pilot hole to a size large enough to safely install the pipe. The reamer is pulled back and rotated while drilling fluid is pumped to cut and remove solids to enlarge the hole. The speed of pre-reaming varies depending on existing soil conditions and the amount of cutting removed from the hole. During the pre-expanding process, bentonite and other additives can form a layer but a high layer on the outside of the hole. This will aid in the stability of the borehole as well as reduce fluid loss or penetration.
Pipe Pull Back
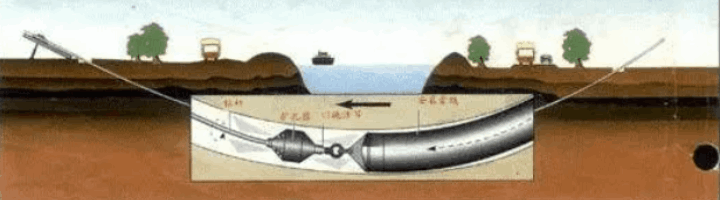
The last step is to pull the pipe back into the pre-reamed hole. The drill pipe and reamer are attached to a swivel which is used between the pipe and reamer to prevent any torsional forces from the rotating drill string from being transferred to the pipe. The pre-reamed holes are enlarged at the front, and bentonite and other additives are used to stabilize the soil layer. As the reaming tool advances through the soil, the pipe is laid underground. Just finished the process of the whole drilling and pulling back at last.
Horizontal Directional Drilling Machine Construction Features
- The whole construction process can be detected, and the direction and depth of drilling can be adjusted at any time.
- Underground directional drilling will not affect road traffic, and will not damage green land, vegetation, and buildings.
- The speed of entering and leaving the site is fast, and the construction site can be adjusted flexibly.
- Suitable for sandy soil, clay, and other ground conditions, but not suitable for high groundwater levels and pebble formation
- The burial depth of the urban pipe network is generally less than 3 meters. When crossing the river, the burial depth is generally 9-18 meters below the river bed.
- Using the principle of pre-expanding, the hole can be re-expanded to the expected diameter step by step according to 1.3~1.5 times the diameter of the pipe when the geology is not clear.
- The adoption of non-excavation construction can reduce a large number of projects. It is conducive to environmental protection and also reduces the cost of infrastructure and ground restoration.
- Using horizontal directional drilling machines for construction can ensure safe and rapid construction work, and reduce construction period and cost.