Rotary screening bucket, also known as excavator screening bucket, is an important excavator attachment. It is mainly used for screening and separating excavated earth and stone materials. Through the use of the excavator screening bucket, the excavated waste slag and impurities can be reduced, the utilization rate of earth and stone materials can be improved, and the workload of subsequent processing of the excavator can be effectively reduced. It is widely used in earthwork engineering, road construction, bridge construction, house construction, and other fields. There are single hydraulic roller buckets for the excavator and double rock screening buckets for the excavator for sale. People can choose the suitable type according to their requirements.
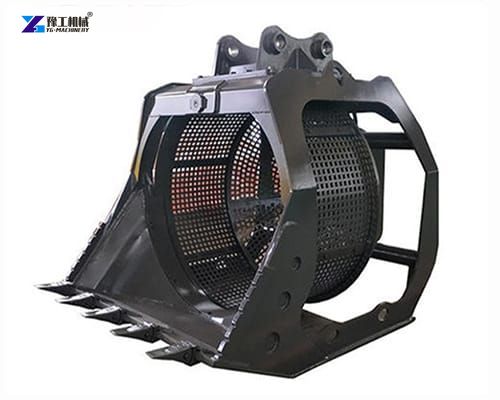
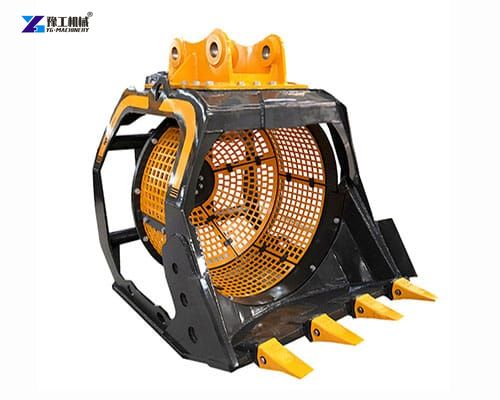
Structure of the Rock Screening Bucket for Excavator
The equipment usually consists of a roller screening bucket, a motor, a reducer, a frame, and other parts. The excavator screening bucket can screen the excavated earth and stone materials when the excavator is working, screen out the granular materials that meet the requirements, and improve the efficiency of engineering operations. The roller bucket is installed on the head of the excavator. The hydraulic motor is connected to the screening bucket through a coupling via a reducer.
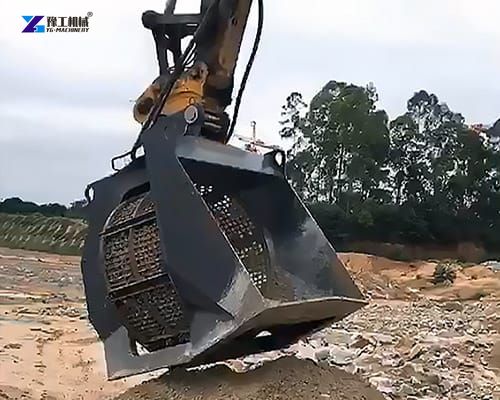
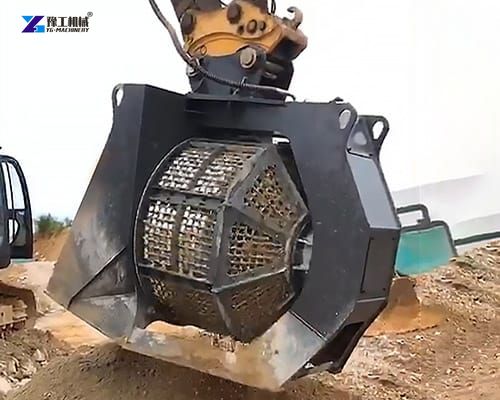
Advantages of the Rotary Screening Bucket
- Large screening area: The roller bucket design has a large screening area and can effectively separate materials of different particle sizes.
- Wide range of applications: It can be used for screening various materials, such as sand, soil, coal, etc., and can meet the needs of different engineering occasions.
- Strong and stable structure: Made of high-quality steel, the structure is strong and stable, with high durability and reliability.
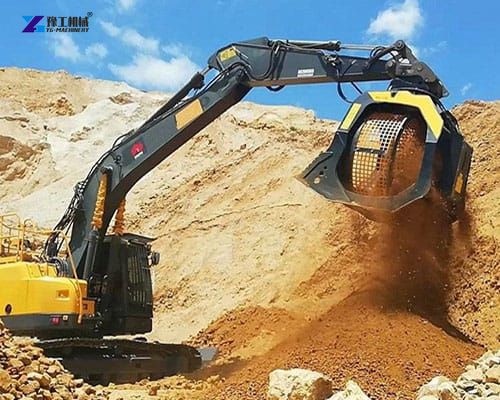
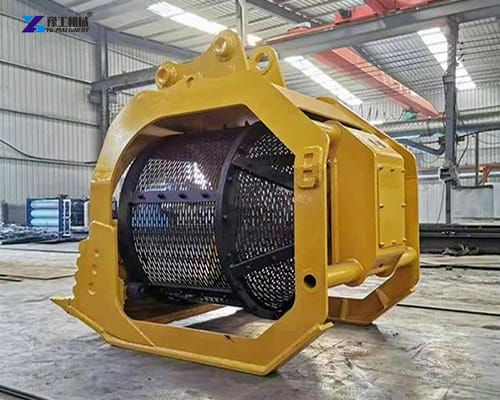
Roller Bucket for the Excavator Characteristics
It achieves material screening through the rotation of the bucket. The high-torque, low-speed hydraulic motor is highly sealed and can work underwater. Different needs can be met by replacing screen plates with different apertures. The machine is welded with high-performance steel plates, which are firmer and not prone to welding and cracking. The high-strength, maintenance-free load-bearing shafts and bearings extend the maintenance cycle, save costs and improve efficiency.
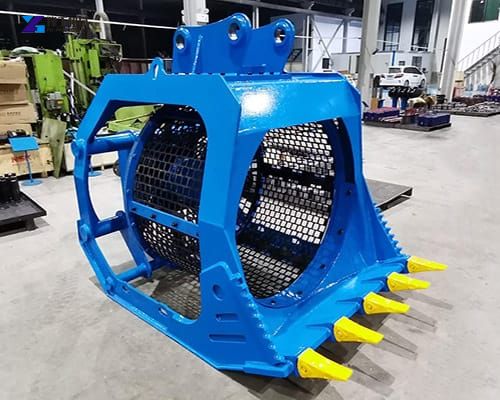
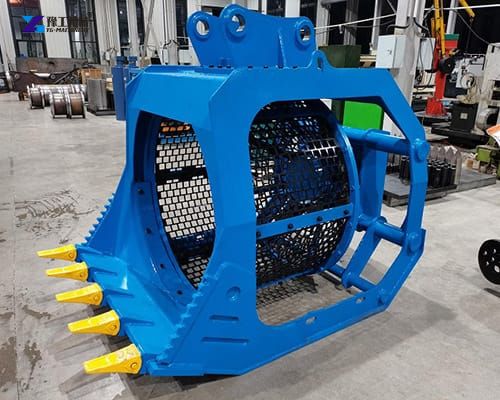
Excavator Attachments for Sale in YG Machinery
As a professional excavator attachments manufacturer, we provide various excavator attachments with different specifications for different uses. We not only have the rock screening bucket but also have the excavator crusher bucket, hydraulic quick hitch, scrap metal shear, excavator rock saw, excavator pile driver, breaker hammer for excavator, pile breaker machine, and so on. Do you need an excavator attachment for your project? If you are interested them above, welcome to contact us for more detailed information.